Precision Leveling Machine with Horizontal Decoiler:
The Perfect Combination for Stress-Free Process Optimization
Marktrodach, Germany – For over a century, DREEFS GmbH Schaltgeräte und Systeme has been a leading name in electromechanical switches. Since 2008, this traditional manufacturer, part of the Everel Group, has specialized in producing high-precision contacts. With an annual output of 500 million contacts for diverse sectors like automotive, household appliances, and healthcare, maximizing efficiency and quality is paramount. How does DREEFS achieve this while operating at peak capacity? The answer lies in smart process optimization, powered by a KOHLER precision leveling machine and a Leicht horizontal decoiler.
The Challenge: Cost Reduction Meets Welding Perfection
DREEFS processes roughly 800 metric tons of copper alloys and 2,700 kg of silver annually for switch contacts. To significantly cut costs, DREEFS strategically shifted the substrate material for many contact parts from half-hard brass to unalloyed DC01 steel. This move alone promised an impressive 90% material cost saving.
However, steel strip demands flawless preparation. Perfect leveling and smoothing are critical to ensure impeccable welding of silver contacts to the substrate. Even a minuscule 0.05 mm distortion could lead to welding defects, posing substantial risks in critical applications like oven switches – a potential fire hazard if a contact fails.
The Solution: KOHLER CPL 120 and Leicht PWL-150 – A Seamless Integration
To conquer this challenge, DREEFS invested in a Leicht Stanzautomation PWL-150 series horizontal decoiler paired with a KOHLER Maschinenbau CPL 120 precision leveling machine. Harald Müller, Managing Director of DREEFS GmbH, highlights the impact: "The switch from brass to steel strips, which generated material cost savings of around 90%, would not have been possible without the CPL 120 from KOHLER. This has made the production process more efficient overall."
Integrating the compact KOHLER leveler into the Leicht horizontal decoiler's control system yielded multiple benefits:
-
Significantly reduced material handling complexity.
-
Substantial space savings.
-
Time efficiency when loading and threading new coils.
-
Dramatic reduction in scrap.
-
Improved welding results.
KOHLER's long-standing reliability also played a key role. A KOHLER leveling machine has been a dependable part of DREEFS' operations since 1979. This proven partnership, combined with Leicht's equally impressive material management solutions, created the optimal production setup.
Precision and Efficiency in Detail
The KOHLER CPL 120 stands out with its compact design and meticulously engineered leveling rollers. Featuring 19 leveling rollers supported by numerous backing rollers, it achieves exceptional rigidity. The small roller diameter ensures precise leveling even for the thinnest strips (from 0.12 mm material thickness) common in the industry. Easy accessibility allows for quick and straightforward cleaning, protecting the strip material from contaminants and extending the machine's lifespan.
The CPL 120 can achieve plastification degrees exceeding 70%, reliably eliminating tension and unevenness in the strip material. This results in a far more stable production process for components meeting even the most stringent precision requirements. Reduced rejects and extended stamping tool service lives further contribute to substantial operational cost savings. "The leveler combined with the horizontal decoiler is simply brilliant," enthuses Thomas Weber, Shift Manager at DREEFS.
Ultimate Quality Assurance Through Industry 4.0
Thanks to the nearly seamless integration of all processes under the Industry 4.0 standard and machine networking via a MARPOSS MES system, DREEFS can trace its entire production – down to individual contact parts and their respective boxes or coils – at any time. All stamping and welding parameters are continuously monitored and recorded. This provides invaluable insights into raw material quality, potential fluctuations, and, crucially, the achieved leveling results – a critical factor for high-speed production of up to 800 welded parts per minute.
This robust quality assurance system ensures defective parts are sorted out or machines halted if deviations from standard parameters occur. This proactive approach prevents costly errors and upholds the high product quality essential for safety-critical applications.
Stress-Free from Start to Finish
The collaboration with KOHLER and Leicht has delivered truly "stress-free process optimization" for DREEFS. The perfectly coordinated machines from both companies are instrumental in optimizing production processes, enabling DREEFS to maintain its high quality standards while significantly boosting efficiency. Looking ahead, as DREEFS explores converting more products from copper alloys to cold-rolled strip for further material cost savings, they will continue to rely on the proven products and excellent partnership with Leicht and KOHLER.
Facts about CPL 120 and the leveling material:
Leveler:
- Torsion-resistant design
- Number of leveling rollers: 19, all leveling rollers supported
- and max. strip width: 10–120 mm
- and max. strip thickness: 0.1–2 mm
- strip cross section: approx. 190 mm2
- and max. yield point: approx. 200–600 N/mm²
- and max. strip speed: 5–30 m/min
Leveling material:
- Copper, steel, aluminum, stainless steel, fully or partially finished strips with precious metals
- Strip thickness: 2 mm
- Strip width: 120 mm
- Tensile strength: 200–600 N/mm2
Curious how KOHLER precision leveling solutions can optimize your manufacturing? Contact us today!
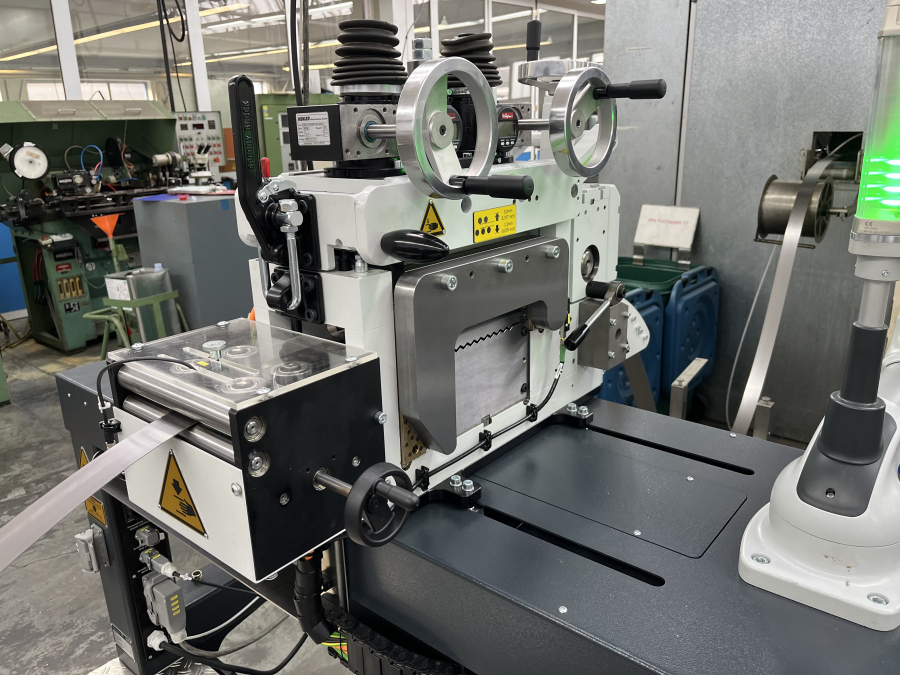