Leading European metalworking company chooses KOHLER 85P.2000 part leveling machine
Low-stress and flat sheets optimize processing
with minimum stress
Precision Sheet Metal Processing through Effective Leveling
Cutting, punching, edge trimming, bending, milling, turning, welding, assembling – at every stage of sheet metal processing, internal stresses in the material can significantly impact the efficiency of production. These stresses, combined with the flatness of the blanks, play a crucial role in determining productivity and quality when manufacturing bent and edged parts, as well as in the assembly of welded structures. Leveled sheets, on the other hand, exhibit minimal stress and the required flatness, ensuring smooth further processing without complications.
These benefits are well understood by EKO MEĐIMURJE d.d., a Croatia-based company specializing in the production of complex sheet metal constructions. Whether it's cabs and tanks for mining machinery from renowned brands like Liebherr, Komatsu, and Caterpillar, or industrial ovens for the food industry, challenges such as extensive rework, welding distortion, and inconsistent results have been eliminated with the introduction of KOHLER part leveling machines.
EKO MEĐIMURJE employs approximately 400 people and processes around 500 tons of steel per month. Its 20,000 m² production facility is equipped with state-of-the-art machinery, including laser cutting systems, various plasma cutting machines, press brakes, 110 welding machines, two robotic welding stations, a Cobot welding robot, multiple machining centers, and a modern paint shop. To further enhance quality and reduce processing times, the company recently integrated a KOHLER Peak Performer 85P.2000 part leveling machine into its production line.
Leveling: Precision Right from the Start
The process of leveling sheet metal using a roll leveling machine consists of a series of repeated bending operations. During this procedure, the material undergoes progressively decreasing alternating bending, generated by offset leveling rollers. This can be visualized as a diminishing sine wave:
- Initially, the material experiences intense alternating bending.
- As it moves through the machine, the bending gradually decreases.
- By the time it exits, the curvature is minimized, leaving the sheet completely flat without springback.
This process ensures the reduction of internal stresses, as areas previously under tension are stretched and compressed beyond their yield point, achieving the required level of stress relief.
Stress-Free Leveling for High-Precision Welded Structures
“Our customers, primarily based in Europe, expect top-quality products. However, the flatness and internal stress levels of the purchased sheet metal often fail to meet the required standards for our processes.
To ensure the highest precision in the manufacture of our steel assemblies, whether for cabs, tanks, or machine parts, we need absolute accuracy. Our largest product to date weighed an impressive 74 tons. Previously, achieving the necessary flatness before welding was an extensive and difficult task.
Our production process required significant manual intervention. Skilled specialists often had to level parts using a torch before they could be precisely welded into assemblies weighing multiple tons. While this approach sometimes yielded satisfactory results, it lacked consistency and significantly slowed down productivity.
We discovered KOHLER through our partners at KARMET BULGARIA LTD., who demonstrated a machine perfectly suited to our needs. After conducting extensive leveling trials with our own parts at KOHLER’s advanced leveling center, we immediately saw remarkable improvements in quality and efficiency, especially in bending and welding operations.
It became clear that this investment would be pivotal for our company’s future. Following a seamless installation process, our Peak Performer 85P.2000 was fully operational by the end of 2023. Since then, alignment work before welding has been drastically reduced, and distortion during welding has been minimized,” explains Zoran Zdolec, Electrical Facilities Manager at EKO MEĐIMURJE d.d.
Optimized Cost-Efficiency with Advanced Features & Functions
Regular cleaning of leveling and support rollers is crucial, especially when processing up to 90% black steel. KOHLER’s Advanced Cleaning System (ACS), an exclusive feature in this machine category, has proven to be a game-changer for EKO.
“With ACS, weekly cleaning is effortless. This prevents contaminants from accumulating on the rollers or the material itself.
The fully retractable leveling cassette allows for quick and easy roller cleaning. This not only improves leveling quality but also significantly extends roller lifespan,” emphasizes Zdolec.
User-Friendly Operation & Outstanding Energy Efficiency
EKO MEĐIMURJE was also impressed by KOHLER’s intuitive operation. The human-machine interface (HMI) and the Expert Calculation System provide a straightforward, user-friendly experience, allowing operators to quickly identify optimal material-specific settings.
Additionally, pre-saved parameters for familiar parts can be accessed instantly, further simplifying operations and boosting efficiency.
Another key advantage is KOHLER’s commitment to energy efficiency and sustainability. The Peak Performer 85P.2000 delivers high performance while maintaining an eco-friendly footprint. Unlike traditional hydraulic levelers, KOHLER machines operate without hydraulics, offering clear benefits:
- Low-maintenance operation
- No risk of leaks
- Resistant to high ambient temperatures
- Exceptional energy efficiency
"The low power consumption is a significant advantage. In standby mode, the machine consumes less than 2 kW, while in idle mode, it uses only 2.5 kW. This efficiency is largely due to KOHLER’s patented electromechanical dynamic gap control and individual direct-drive rollers.
Instead of using a large distribution gear, each roller is powered by a dedicated drive with planetary gearing, ensuring consistent, high-quality results—even for complex geometries,” Zdolec highlights.
Conclusion: A Smart Investment
With the KOHLER Peak Performer 85P.2000 part leveling machine, EKO MEĐIMURJE has achieved:
- Superior quality and process stability
- Minimal rework and reduced material waste
- More efficient welding and bending operations
- Lower energy consumption and operating costs
“All in all, we are extremely satisfied. The results confirm that this was the right investment. The part leveling machine will pay for itself in a short time, helping drive the future success of our company,” concludes Zdolec.
Part leveling machine at EKO MEĐIMURJE d.d.:
- Peak Performer 85P.2000
- The leveled sheets are primarily of blackplate
- Width of the sheets: up to 2,000 mm
- Material thickness of the sheets: up to 28 mm
- Advanced cleaning system
- Patented electromechanical dynamic gap control
- Intelligent overload protection
- Pinch-off edge protection
- Easy-Feed
- Direct drive
- Intuitive user interface
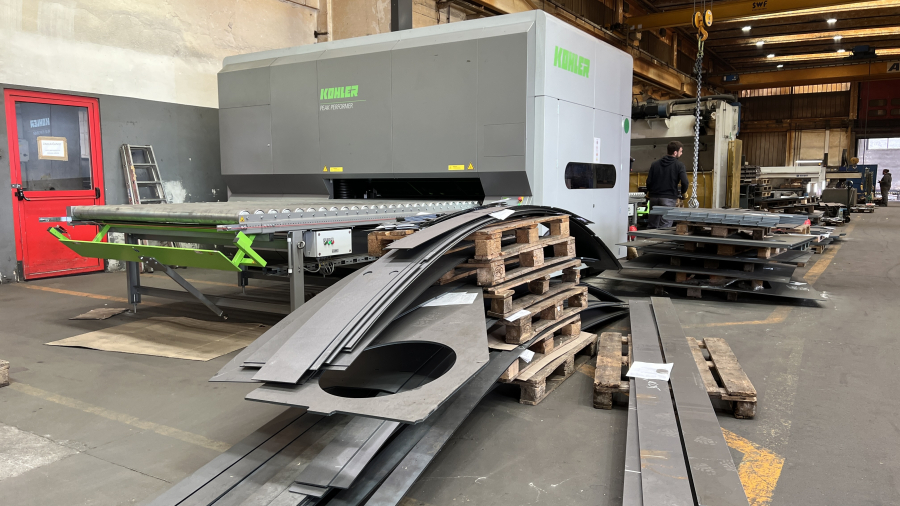